7 Common Powder Coating Problems and How to Prevent Them
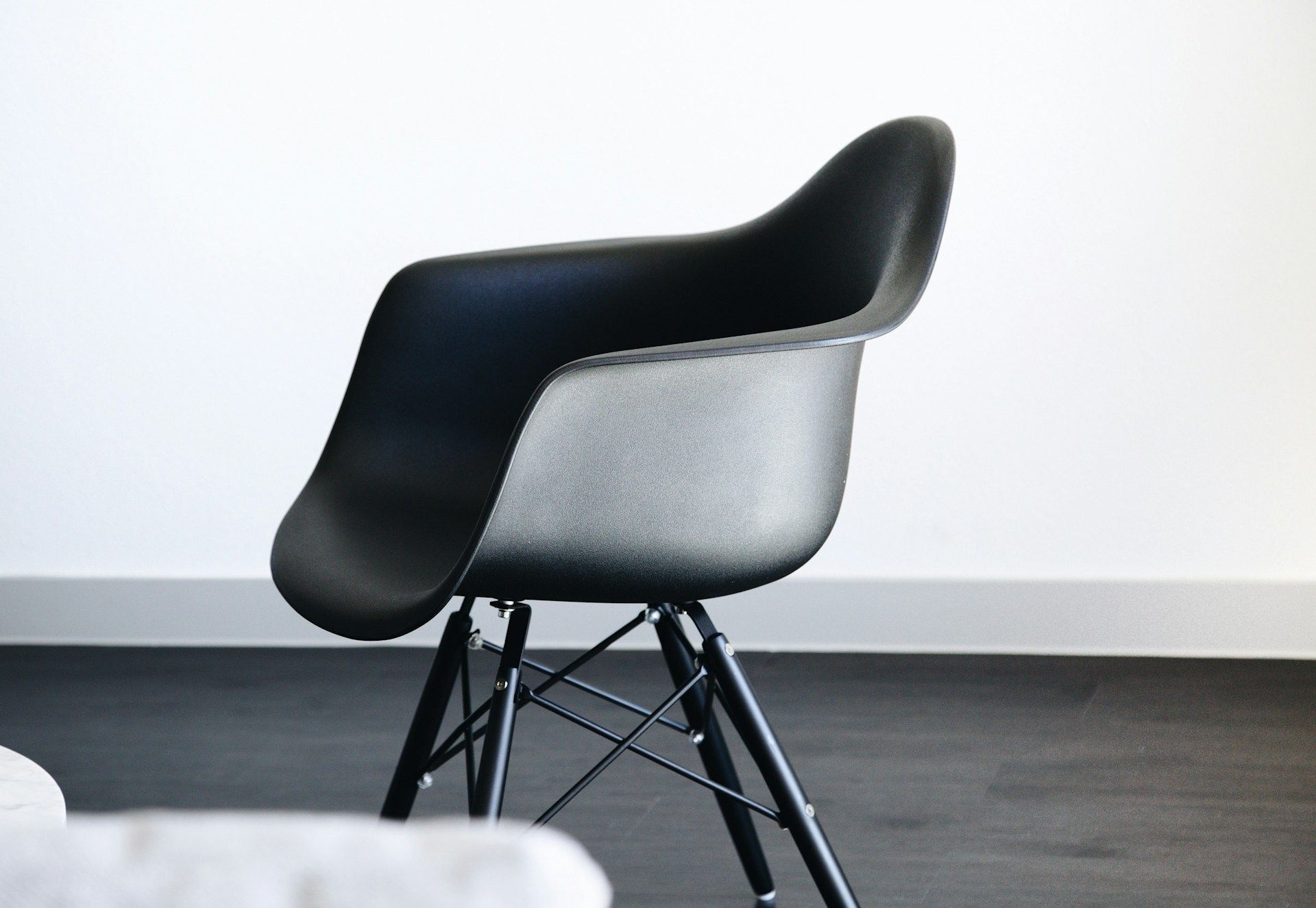
Powder coating has become a preferred finishing method for numerous industries due to its durability, environmental benefits, and exceptional appearance. However, like any process, powder coating can come with its own challenges. Understanding the common problems that may arise and learning how to prevent and troubleshoot them is crucial to achieving the best possible results from your powder coating projects.
In this article, we will shed light on seven common powder coating problems, including their causes, and provide valuable expert advice on prevention and troubleshooting techniques to optimize the quality and durability of your powder-coated finishes. Whether you are an industry professional or simply considering powder coating for your products, this guide will help you navigate potential setbacks and ensure a successful outcome for your project. Read on to deepen your understanding of common powder coating concerns and enhance your skills in this in-demand finishing process.
1. Incomplete or Uneven Coverage
One common powder coating problem is incomplete or uneven coverage of the coated surface. This issue can be caused by multiple factors, such as insufficient electrostatic charge, improper spraying technique, poor grounding, or inadequate cleaning and pretreatment of the substrate.
To prevent incomplete or uneven coverage:
- Ensure that the electrostatic spray gun is functioning correctly and that the voltage settings are appropriate for the specific powder being used.
- Train operators on proper spraying technique, including consistent distance and angle between the gun and the part.
- Check for proper grounding, as inadequate grounding can lead to poor transfer efficiency and uneven coverage.
- Thoroughly clean and pretreat parts to remove impurities and promote good adhesion.
2. Orange Peel Finish
The orange peel effect is characterized by an uneven surface with a texture resembling the skin of an orange. This issue can arise due to several factors, such as incorrect powder formulation or viscosity, inadequate curing, and too high or low film thickness.
To prevent an orange peel finish:
- Check that the powder's specific gravity and reactivity are suitable for the part being coated.
- Ensure that all equipment, including the oven and spray guns, are functioning correctly and set to the appropriate settings.
- Measure film thickness and adjust application technique or equipment settings if too high or too low.
- Allow sufficient time for curing and follow the manufacturer's guidelines for temperature and dwell time.
3. Pinholes and Outgassing
Pinholes and outgassing refer to tiny holes or bubbles that appear on the coated surface, usually caused by trapped air or moisture during the baking process. This issue typically occurs when the substrate contains porosity or when contaminants are present on the surface.
To prevent pinholes and outgassing:
- Thoroughly clean and degrease the part to eliminate contaminants and moisture.
- Follow proper pretreatment procedures, such as phosphating or abrasive blasting, to enhance adhesion and reduce porosity.
- Apply a primer designed for porous substrates to reduce air or moisture entrapment.
- Increase the curing time or temperature to allow for sufficient outgassing before the topcoat is fully cured.
4. Chipping and Poor Adhesion
Chipping and poor adhesion occur when the powder coating does not bond correctly to the substrate, leading to the coating flaking or peeling off. Factors that contribute to this issue include inadequate cleaning and pretreatment, low-quality powder, improper curing, or poor handling and storage of coated parts.
To minimize chipping and poor adhesion:
- Ensure thorough cleaning and pretreatment of parts to remove contaminants, rust, or oils that can compromise adhesion.
- Use high-quality powder materials with appropriate properties for the specific application.
- Follow the manufacturer's guidelines for curing times and temperatures, as inadequate curing can impact adhesion.
- Store and handle finished parts with care to avoid chipping or damaging the coating.
5. Intercoat Delamination
Intercoat delamination occurs when multiple layers of powder coating do not bond properly, resulting in separation or peeling between layers. This problem often arises from inadequate surface preparation, compatibility issues between coating materials, or incorrect curing.
To prevent intercoat delamination:
- Ensure that substrate surfaces are clean, free of contaminants, and properly prepared for the application of multiple coats.
- Verify that the different coating materials are compatible and use products designed for multi-layer applications.
- Follow the recommended curing schedule for each layer, allowing for adequate time between coats to prevent premature curing.
6. Faraday Cage Effect
The Faraday cage effect refers to the difficulty in achieving even coverage of powder coating in corners, recesses, or other complex geometric areas due to the shielding effect of the electrostatic field. This can result in thin or non-existent coverage in certain areas, compromising the appearance and durability of the finish.
To minimize the Faraday cage effect:
- Adjust the electrostatic spray gun settings, such as voltage or current, to improve the penetration of the powder into recessed areas.
- Employ proper gun positioning and spraying techniques designed for complex geometries.
- Use manual or robotic pre-programmed spraying sequences optimized for the part's geometry.
- Consider applying a conductive primer or a pre-heated part to increase coverage in challenging areas.
7. Color Mismatch
Color mismatch is a common problem in powder coating when the final color does not match the desired or specified color. Factors that can contribute to color mismatch include lighting conditions, substrate material, powder formulation, and curing process.
To prevent color mismatch:
- Inspect the coated part under different lighting conditions, such as natural daylight, fluorescents, or LEDs, to ensure accurate color reproduction.
- Verify that the powder formulation is correct and that the supply is consistent in color and quality.
- Follow the manufacturer's recommended curing parameters, as deviations in time and temperature can impact the final color appearance.
- Request color samples or swatches for approval before coating the production parts.
Achieve Flawless Powder Coating with Coast 2 Coast
When it comes to powder coating, understanding the common challenges and best practices for prevention and troubleshooting is essential. Coast 2 Coast Powder Coating is committed to helping you navigate these issues and achieve stunning, durable finishes for your products and projects.
By partnering with our team of experts, you can ensure that your parts receive the highest quality powder coating services that exceed industry standards. From proper cleaning and pretreatment to accurate color matching and expert application techniques, Coast 2 Coast Powder Coating has the experience and knowledge to make your project a success.
Ready to embark on your powder coating journey with confidence? Contact Coast 2 Coast Powder Coating today to discuss your unique requirements and discover how our professional services can bring your vision to life while avoiding common powder coating pitfalls.