Overcoming Powder Coating Obstacles: Identifying and Addressing Common Defects
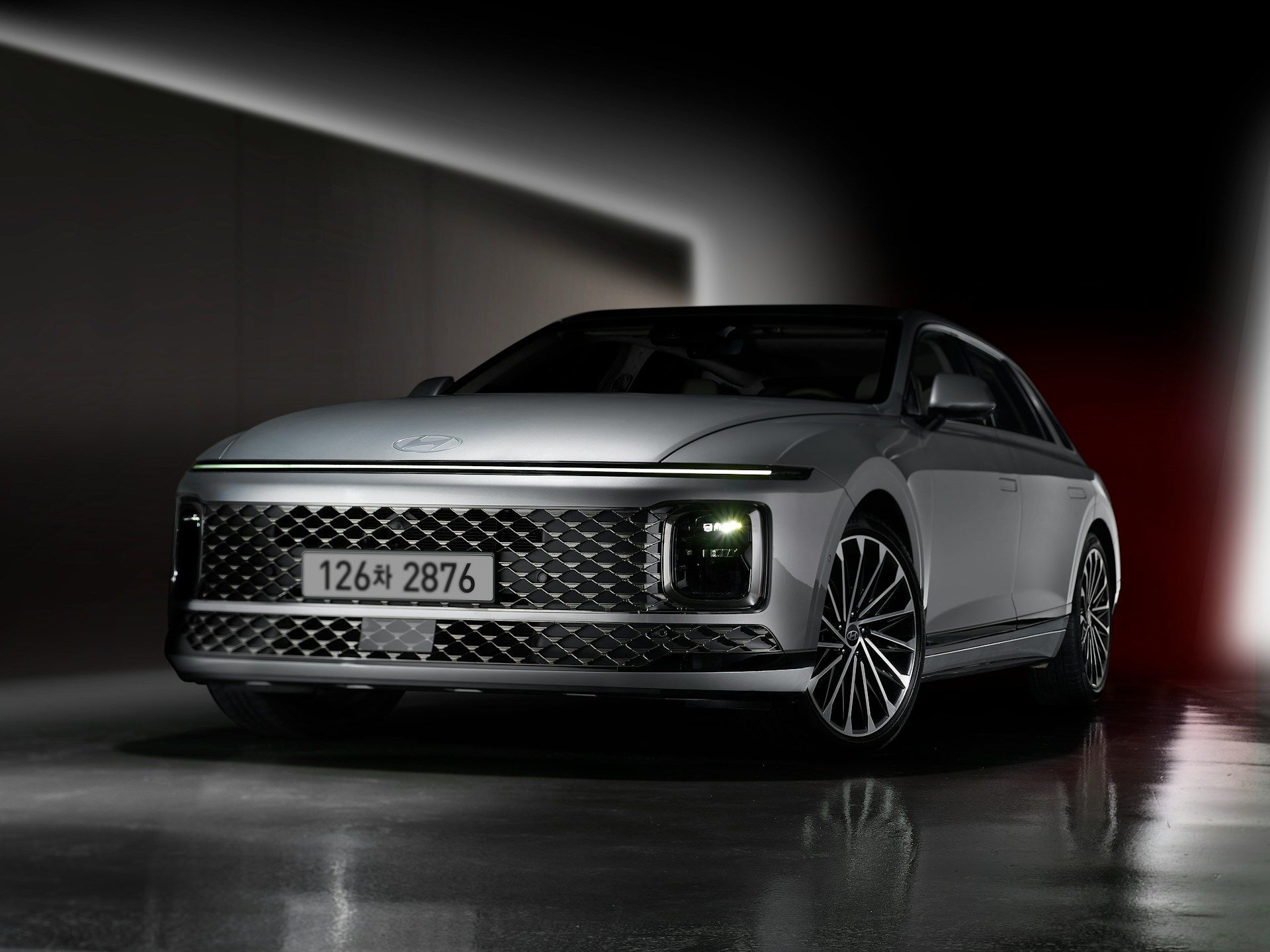
Powder coating has become the go-to finishing solution for countless industries owing to its superior durability, visual appeal, and environmental sustainability. However, like any intricate process, powder coating can occasionally present challenges in the form of defects that may compromise the quality and longevity of the final result. Understanding the potential sources of these imperfections and how to prevent or remedy them is crucial for ensuring a successful powder coating experience.
In this comprehensive guide, we will dive into the world of common powder coating defects, exploring their causes, prevention strategies, and solutions. From inadequate surface preparation and poor adhesion to orange peel, pinholes, and more, we will examine the multitude of factors that can contribute to powder coating imperfections and arm you with the knowledge to overcome these challenges.
At Executive Coast 2 Coast Powder Coating, our team prides itself on delivering top-tier powder coating services by addressing and resolving potential issues before they become problematic. In partnering with us, you can trust that our proactive and detail-oriented approach will result in a flawless, high-quality finish for your projects. By gaining a deeper understanding of common powder coating defects, you can make informed decisions and work collaboratively with us to achieve the exceptional outcomes that your projects deserve.
1. Insufficient Surface Preparation: Laying the Foundation for a Flawless Finish
Arguably the most significant contributor to powder coating defects is inadequate surface preparation. Surface preparation is a critical step in the powder coating process, as it determines how well the coating will bond with the substrate. Some common issues arising from improper surface preparation include:
- Poor Adhesion: If a surface is inadequately cleaned or prepared, the powder coating may not bond properly, leading to issues such as delamination, peeling, or chipping.
- Surface Contamination: Any remaining contaminants on the surface, such as oils, dirt, or dust, can negatively affect the powder coating's adherence and overall appearance.
- Outgassing: If a substrate has not been appropriately degassed or pre-baked, trapped gases may escape during the curing process, resulting in pinholes or blisters in the final finish.
Prevention and Solutions:
- Thoroughly clean and degrease the surface to remove contaminants.
- Use appropriate chemical or mechanical surface preparation methods, depending on the substrate.
- Pre-bake or degas substrates prone to outgassing to release trapped gases prior to powder coating.
2. Misaligned Equipment and Application Technique: Ensuring Precision in Powder Application
The effective application of the powder coating material is another essential factor in achieving high-quality results. Issues can arise from equipment-related problems or improper application techniques, such as:
- Inconsistent Thickness: Uneven application of the powder coating can lead to variations in thickness, causing inconsistencies in the appearance and performance of the finished product.
- Orange Peel: Uneven or rough surface texture resembling the skin of an orange, often resulting from excessive powder buildup or incorrect spray gun settings.
- Faraday Cage Effect: Difficulty in achieving proper coverage in recessed areas, corners, or intricate geometries due to the electrostatic properties of the powder coating process.
Prevention and Solutions:
- Regularly inspect, clean, and maintain spray equipment to ensure optimal performance.
- Use proper application techniques and adjust spray gun settings as needed for uniform coverage.
- Apply multiple coats to hard-to-reach areas or consider manual powder coating for complex geometries.
3. Curing Process Inconsistencies: Achieving a Robust and Long-lasting Finish
The curing process is crucial for solidifying the bond between the powder coating and the substrate, forming a robust and protective finish. However, inconsistencies in the curing process can lead to several defects, such as:
- Discoloration: Inaccurate temperature settings or uneven heat distribution can cause changes in the intended color or appearance of the powder coating.
- Blisters or Bubbles: Insufficient curing time, temperature, or airflow can result in trapped solvents or moisture, causing blisters or bubbles to form in the finished coating.
- Cracking or Chipping: An overbaked or underbaked powder coating may become brittle, more susceptible to cracking, or lack the desired flexibility and durability.
Prevention and Solutions:
- Monitor and maintain curing oven settings to ensure even heat distribution, proper oven temperature, and necessary curing time.
- Verify proper airflow within the curing oven to minimize the risk of moisture or solvent entrapment.
- Regularly assess the condition of curing oven components, such as heating elements or fans, to maintain optimal performance.
4. Powder Coating Material Quality: Selecting the Best Products for Your Project
The quality of the powder coating material plays a vital role in the overall performance and appearance of the finished product. Issues can arise when substandard materials are used or improperly stored, such as:
- Lumping or Clogging: Poor-quality powders or those exposed to moisture may form lumps or clog the spray equipment, resulting in an uneven or inconsistent application.
- Poor Flow and Leveling: Low-quality powders may not flow and level properly during the curing process, causing surface imperfections or visually unappealing finishes.
- Reduced Performance: Inferior materials may compromise the durability, color stability, or corrosion resistance of the powder coating, ultimately impacting the longevity of the finished product.
Prevention and Solutions:
- Source powder coating materials from trusted suppliers with a track record of providing high-quality products.
- Follow the manufacturer's recommendations for storage and handling of powder coating materials.
- Regularly inspect powder materials for signs of contamination, spoilage, or compromised quality before application.
Proactively Tackling Powder Coating Defects for Exceptional Results
A thorough understanding of common powder coating defects, their causes, and effective prevention or remediation strategies is essential for ensuring a high-quality and visually appealing finish. By proactively addressing potential issues in surface preparation, equipment and application technique, curing process, and material quality, you can confidently achieve the outstanding results that powder coating has to offer.
At Executive Coast 2 Coast Powder Coating, our knowledgeable and experienced team is dedicated to delivering top-tier
powder coating services that consistently exceed expectations. Allow our expertise and commitment to quality to guide you on your journey to stunning, durable, and long-lasting finishes, demonstrating the exceptional potential of skillfully executed powder coating.