The Powder Coating Process: A Step-by-Step Guide to Achieving a Flawless Finish
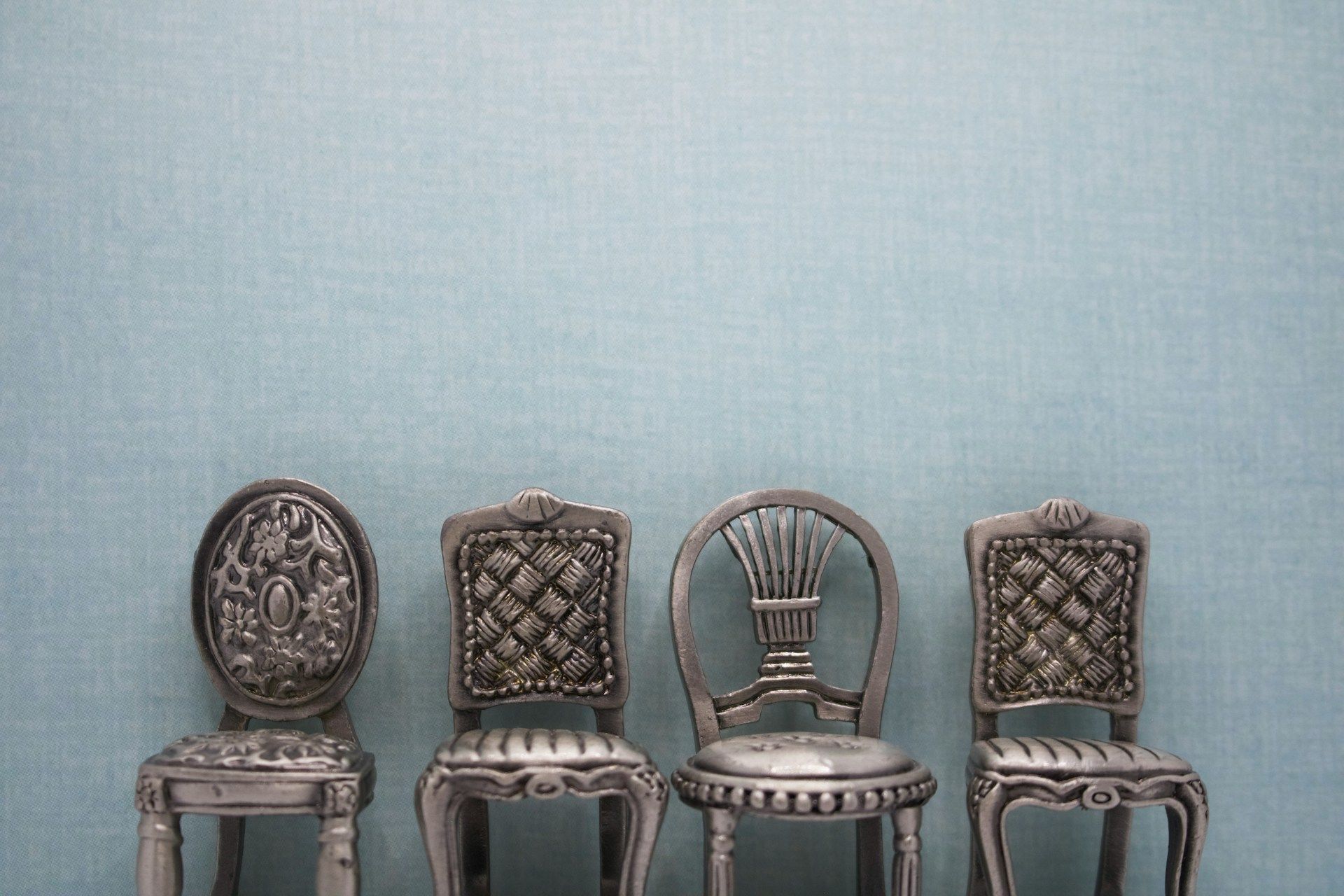
Powder coating has gained widespread recognition and admiration for its ability to transform and protect various surfaces, delivering a durable and visually appealing finish that sets it apart from traditional paint applications. By offering countless colors, finishes, and textures to choose from, powder coating has become an indispensable solution in industries ranging from automotive to furniture and architecture. However, understanding the intricacies of the powder coating process is essential for ensuring exceptional results and maximizing the potential of this innovative finishing technique.
In this comprehensive guide, we will demystify the powder coating process by breaking it down into its essential steps and providing an in-depth understanding of each stage. From the crucial surface preparation to the electrostatic application of the powder and, finally, to the curing process responsible for creating a robust, protective finish, you will gain valuable knowledge and insights into how powder coating is carefully executed, yielding a flawless result.
At Executive Coast 2 Coast Powder Coating, our team of experts has honed their skills through years of experience, enabling them to offer top-tier powder coating services for a wide array of applications. As you embark on this educational journey, our hope is that you will develop an appreciation for the precision and artistry involved in the powder coating process.
1. Surface Preparation: The Key to a Long-Lasting and High-Quality Finish
The first and arguably most crucial step in the powder coating process is the thorough preparation of the surface to be coated. Proper surface preparation is essential for ensuring a strong bond between the coating and the substrate, ultimately resulting in a durable and long-lasting finish. The surface preparation process typically involves the following stages:
- Cleaning: Removal of dirt, grease, and other contaminants through degreasing and cleaning solutions. This step is vital for ensuring that the powder coating adheres effectively to the surface.
- Stripping: If previously coated or painted, the surface must be stripped of any existing finish. Methods used for stripping include chemical stripping, sandblasting, or media blasting.
- Etching: For certain materials, such as aluminum, an etching process may be necessary to create a corrosion-resistant conversion coating that promotes optimal adhesion.
- Rinsing and Drying: After the previous steps have been completed, the surface must be thoroughly rinsed and dried to prevent any residual contaminants or moisture from interfering with the adhesion process.
2. The Electrostatic Application Process: Expertly Distributing the Powder Coating Material
Once the surface has been meticulously prepared, the next stage in the powder coating process is the application of the powder material. This step requires precision and skill to achieve a uniform and comprehensive coverage of the surface. The most common method for applying powder coating is electrostatic spray deposition (ESD), in which the following steps take place:
- Charging the Powder: The powder coating material is fluidized and then propelled through a spray gun, which imparts an electrostatic charge to the particles. This charge helps the particles adhere to the substrate, ensuring a comprehensive and even application.
- Applying the Powder: The charged powder particles are sprayed onto the surface, adhering to it due to the electrostatic attraction between the particles and the grounded substrate. The highly controlled spray process allows for precise application, resulting in a consistent and uniform coating.
- Thickness Control: Depending on the desired thickness of the final coating, multiple passes with the spray gun may be necessary, building up the powder layer to the optimal thickness for performance and appearance.
3. Curing Process: Fusing the Powder Coating to the Substrate
After the powder material has been evenly applied to the surface, the coated part must undergo a curing or "baking" process to harden the coating and create a strong, resilient finish. During the curing process, a chemical reaction occurs between the coating and the substrate, resulting in a durable bond that resists chipping, cracking, and peeling. The curing process includes the following steps:
- Transfer to the Oven: The coated part is carefully transferred to a curing oven, ensuring that the powder remains undisturbed and maintains uniform coverage throughout the process.
- Optimal Temperature and Time: The curing temperature and duration must be carefully calibrated for the specific powder coating material and substrate used. These factors are closely monitored to ensure that the coating cures properly without overbaking or underbaking.
- Cooling and Hardening: Once the curing process is complete, the part must be allowed to cool gradually, allowing the coating to harden and achieve its final robust and protective quality.
4. Quality Control and Inspection: Ensuring a Flawless Final Result
The final step in the powder coating process involves a thorough inspection and quality control assessment of the coated part or component. This evaluation is critical for ensuring that the powder coating has been applied correctly and performs as intended, providing a durable and visually appealing finish. Key aspects of the quality control and inspection process include:
- Visual Inspection: The coated part is visually examined for any imperfections, such as uneven coverage, blotchiness, or other texture issues. Any flaws must be addressed before the part is considered complete.
- Thickness Measurement: The thickness of the cured powder coating is measured using specialized equipment to ensure that it meets the desired specifications and performance requirements.
- Adhesion Testing: Adhesion tests, such as the crosshatch or pull-off test, may be conducted to confirm that the powder coating has bonded securely to the substrate, ensuring a long-lasting finish.
Understanding the Powder Coating Process to Achieve Outstanding Results
By familiarizing yourself with the step-by-step process of powder coating, you can better appreciate the artistry, precision, and expertise required to achieve exceptional results. Through diligent surface preparation, skillful electrostatic application, meticulous curing, and comprehensive quality control, powder coating delivers a stunning, durable, and long-lasting finish for a wide array of applications.
At Executive Coast 2 Coast Powder Coating, our team of professionals is committed to providing top-tier
powder coating services that reflect our dedication to quality, performance, and customer satisfaction. Allow us to put our expert knowledge and skills to work for you, transforming your projects with the unparalleled benefits of a flawlessly executed powder coating finish. Contact us today.